Sage ceased all support and services for Sage Manufacturing in September 2021. Since then, Sage have partnered with Sicon and now recommend the Sicon Manufacturing suite as their solution of choice for the UK SME Manufacturing market
What is Sicon Manufacturing?
Sicon Manufacturing is a set of additional, easy to use modules for Sage 200 that allow the entire manufacturing process to be encompassed within the Sage 200 suite. Features found in Sicon Manufacturing include: Job Costing, Works Order Processing, Estimating and Capacity Planning, Material Planning, Resource Planning and Labour Recording.
These features seamlessly integrate with the Sage 200 Stock, Bill of Materials, Sales and Purchase Order Processing modules to provide a complete overview of the manufacturing process using only 1 software interface.
Why use Sicon Manufacturing for Sage 200?
Firstly, Sicon Manufacturing is available for all Sage 200 users based on permissions at no extra cost! It also boasts many features that allow manufacturing businesses to easily keep track of their workflow processes.
Many manufacturing businesses rely on spreadsheets to keep track of their business procedures, however, as a business grows, a greater level of traceability is required that spreadsheets simply can’t provide.
On the other hand, Sicon Manufacturing provides full resource visibility, complete stock traceability and overall business clarity.
How will Sicon Manufacturing help your business?
The integrated nature of Sicon Manufacturing allows efficient resource planning at every stage of the production process – from job costing to material planning to purchase order processing.
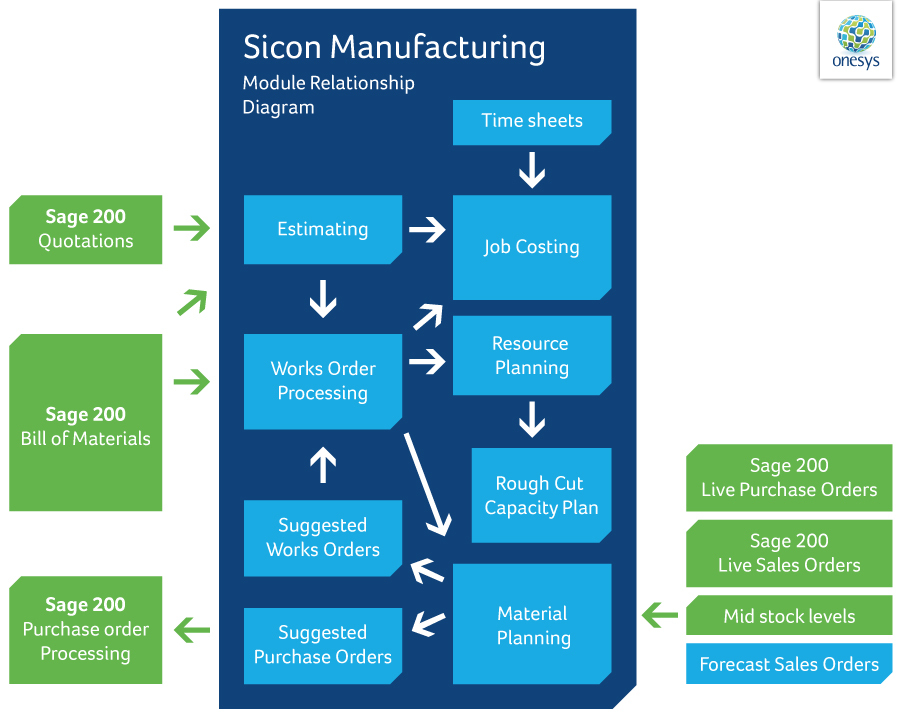
Here’s a more in-depth look at how some of the Sicon Manufacturing features can solve common business issues:
Stock Traceability
The larger a business grows, the more traceability is required. Sicon Manufacturing has the capability to track batch/serial numbers on goods received as well as on completed stock items. It can also track products that have been sold and shipped, and what components were used during the assembly process, allowing users to plan ahead and order more materials if required.
This level of visibility is crucial for growing businesses as it allows business departments to work together, access data in real-time and means any errors can easily be traced.
Manageability
If you are a current Sage 200 user, then Sicon Manufacturing can be integrated with ease. The software retains the Sage 200 Bill of Materials module at its core, meaning data is just as easily accessed as before.
Sicon Manufacturing also provides an incredibly powerful Material Planning module that pulls data from every area of the Sage system, quickly identifying resource requirements. With just a few clicks, Works Orders and Purchase Orders can be created using the data that has been gathered. Sicon Manufacturing provides ease of use and removes the need for lengthy ordering processes.
Planning
While the Material Planning module makes inventory recommendations, Sicon’s Capacity Planning module allows users to create a capacity plan at labour and machine level to ensure Works Orders are completed on time. Users can create departments and input staffing levels and machine run times to generate detailed work plans against Works Orders.
Time sheets can also be imported into the Capacity Planning module, and Sales Orders and Over Capacity reports can be generated, which help keep businesses on track.
Precision
By integrating all business processes into one central hub, Sicon Manufacturing provides users with absolute clarity over their entire business endeavours. Users can look up precise, real-time data from any department to ensure manufacturing processes are up-to-date and on-track.
Sicon Manufacturing pulls together information from Sage 200 and the additional 7 Sicon modules to provide total business visibility.
The Sicon Manufacturing Projects module integrates and collates real-time data from Sage Sales Order Management, Purchase Order Management, Purchase Ledger, Stock, Works Order Processing and Time Recording, giving precise and timely project updates and providing full visibility of the project’s profitability.
Other Sicon Manufacturing Features
Along with its standard in-built functionalities, Sicon Manufacturing also has the capability to connect to other modules to further enhance the production process.
Additional features include:
- Shop Floor Data Capture can be achieved by purchasing the Sicon WAP Timesheet module. This will provide options for Works Order component amendments and labour bookings.
- WAP Timesheets allows staff to log flexible work patterns directly into the system. This information is then used to allocate time against specific jobs and activities.
Contact Us
If you’d like to know more about how Sicon Manufacturing integrates with Sage 200, please call us on 01423 330335, or email us at
sales@onesys.co.uk.